From Traditional to Digital: Phased Strategy for Manufacturing Innovation
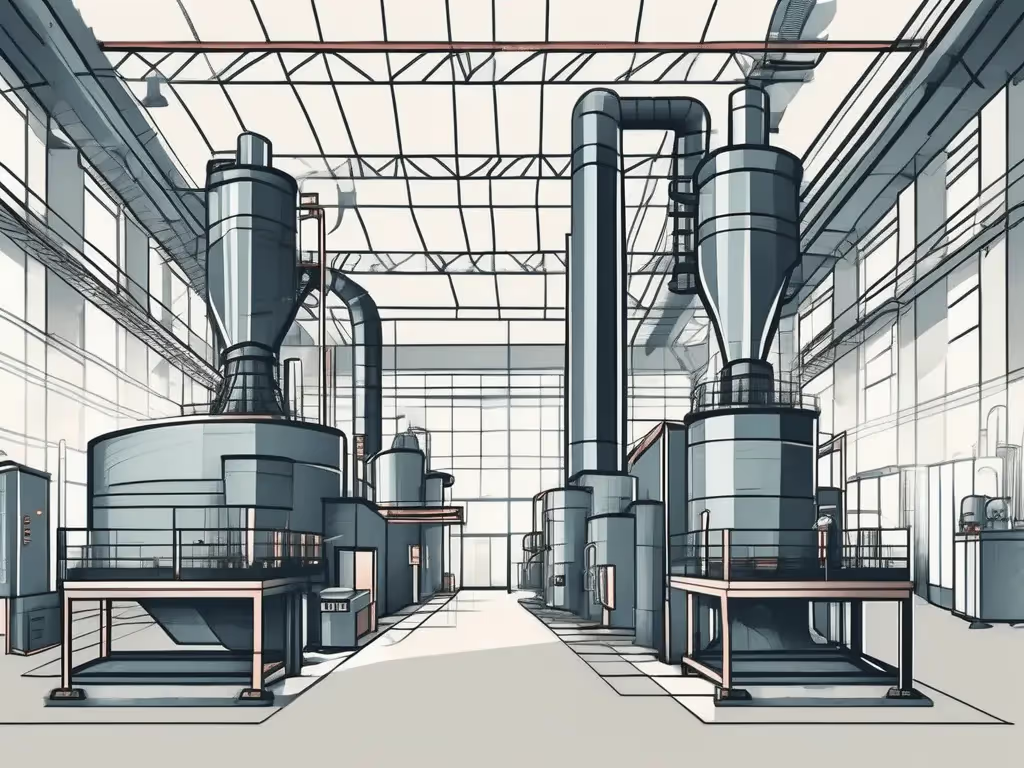
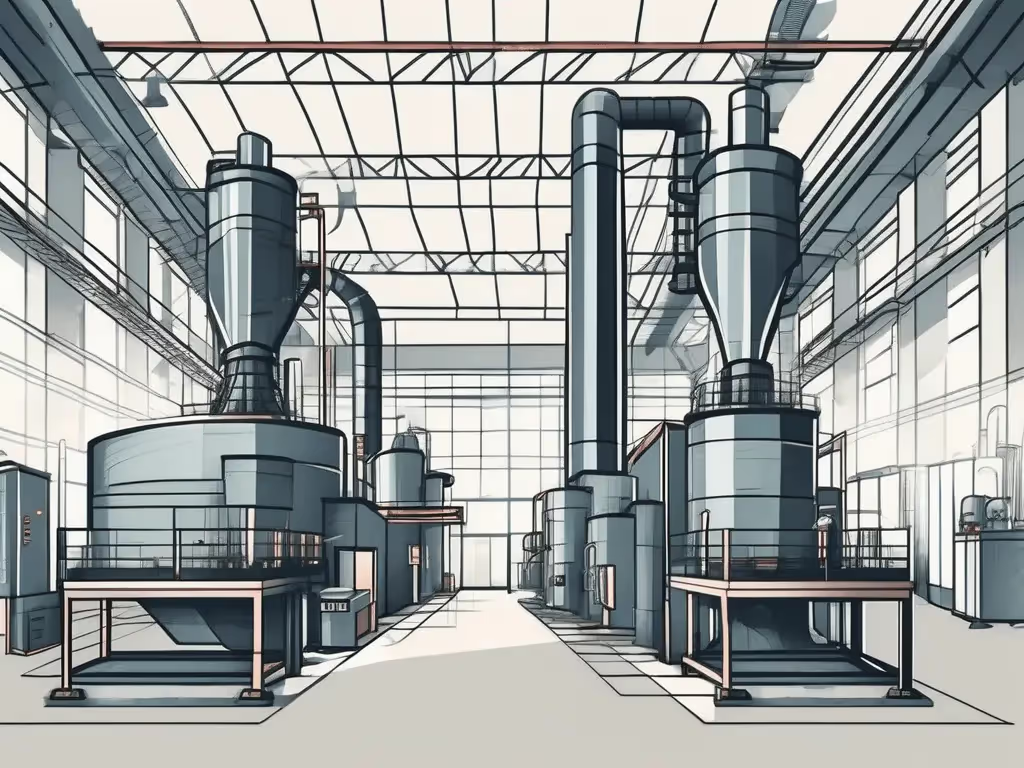
Manufacturing has always been an essential component of global economies, constantly evolving to meet changing demands and technological advancements. In recent years, digital transformation has become a buzzword in the industry, promising improved efficiency, increased productivity, and reduced costs. However, transitioning from traditional to digital manufacturing is not a one-step process but rather a phased strategy that involves careful planning and implementation. In this article, we will explore the various stages of this transformation and discuss key considerations for successful adoption.
The Evolution of Manufacturing Processes
Over the years, manufacturing processes have evolved from manual labor to mechanization and automation. These advancements have significantly increased productivity and output. However, with the rise of digital technologies such as the Internet of Things (IoT), artificial intelligence (AI), and robotics, a new era of manufacturing innovation has emerged. Manufacturers are now able to leverage these technologies to streamline operations, optimize supply chains, and improve overall performance.
Digital transformation in manufacturing is a multifaceted process that involves not only the adoption of cutting-edge technologies but also a fundamental shift in organizational culture and business practices. Companies that successfully navigate this transformation often find themselves reaping the benefits of increased productivity, reduced operational costs, and improved product quality.
Furthermore, the implementation of digital solutions can lead to enhanced supply chain management, streamlined production processes, and the ability to quickly adapt to changing market demands.One key aspect of digital transformation in manufacturing is the concept of smart factories, where interconnected systems and machines communicate with each other in real time. This interconnectedness allows for predictive maintenance, where machines can anticipate when they will need servicing, thus minimizing downtime and maximizing efficiency.
Assessing the Current State of Manufacturing Technology
Before embarking on a digital transformation journey, manufacturers need to assess their current technological capabilities and infrastructure. This involves conducting a comprehensive audit of existing systems, equipment, and software to identify gaps and areas that need improvement. It is important to have a clear understanding of the organization's strengths and weaknesses to develop an effective strategy for implementation.
During the assessment process, manufacturers should also consider the integration of Internet of Things (IoT) devices to enhance connectivity and data collection on the factory floor. IoT sensors can provide real-time insights into machine performance, production efficiency, and predictive maintenance needs. By leveraging IoT technology, manufacturers can optimize operations and streamline processes for increased productivity
Implementing a Step-by-Step Approach to Innovation
A phased approach to manufacturing innovation allows organizations to manage risks and minimize disruption. Rather than implementing drastic changes overnight, manufacturers can break down the transformation process into smaller, manageable steps. This approach enables organizations to gradually integrate digital technologies while ensuring minimal disruption to ongoing operations.
One key benefit of adopting a step-by-step approach to innovation is the ability to gather feedback and make adjustments along the way. By breaking down the transformation process into smaller phases, organizations can assess the impact of each change and make necessary modifications before moving on to the next step. This iterative approach not only helps in fine-tuning the innovation strategy but also ensures that the final outcome aligns with the organization's goals and objectives.
Overcoming Challenges in Transitioning to Digital Manufacturing
Transitioning from traditional to digital manufacturing is not without challenges. One of the main obstacles is resistance to change from employees. To overcome this, organizations must invest in training and upskilling programs to ensure the workforce is prepared for the digital era. Additionally, there may be financial implications to consider, as implementing new technologies can require significant upfront investments. Adapting existing processes and workflows to accommodate digital technologies may also pose logistical challenges that need to be addressed.
Leveraging Data and Analytics for Improved Efficiency
Data is at the heart of digital manufacturing. By collecting and analyzing real-time data from various sources, manufacturers can gain valuable insights into their operations and make data-driven decisions. Advanced analytics tools can help identify areas for improvement, optimize production schedules, and predict maintenance needs. This data-driven approach leads to improved efficiency, reduced downtime, and increased overall productivity.
Training and Upskilling the Workforce for the Digital Era
As manufacturing processes become increasingly automated, the role of the workforce is also evolving. Employees must acquire new skills to operate and maintain digital technologies effectively. Providing comprehensive training programs and upskilling opportunities is vital to ensure a smooth transition. By investing in the workforce, organizations can create a culture of innovation and empower employees to embrace and leverage digital technologies.
Measuring Success: Key Performance Indicators for Innovation
When embarking on a digital transformation journey, it is crucial to define and measure success. Key Performance Indicators (KPIs) enable organizations to track progress and evaluate the impact of digital technologies on their operations. KPIs may include metrics such as overall equipment effectiveness, cost savings, quality improvements, and customer satisfaction. Regular evaluation and adjustment of KPIs help organizations stay focused on their goals and make informed decisions.
Case Studies: Successful Implementation of Digital Strategies
Real-world examples of successful digital transformation can provide valuable insights and inspiration. Case studies from various industries showcase how organizations have leveraged digital technologies to drive innovation and achieve significant results. By studying these success stories, manufacturers can learn from best practices and tailor their own strategies to suit their specific needs and goals.
Looking Ahead: Future Trends in Manufacturing Innovation
As technology continues to advance, manufacturing innovation will continue to evolve. Industry 4.0, with its focus on interconnected systems and intelligent manufacturing, represents the next phase of digital transformation. Emerging technologies such as 3D printing, blockchain, and virtual reality are also expected to disrupt traditional manufacturing processes. Manufacturers should stay informed about these trends and proactively explore ways to integrate new technologies into their operations.
In conclusion, the journey from traditional to digital manufacturing is not a straightforward path but rather a phased strategy that requires careful planning and implementation. By embracing digital transformation, manufacturers can improve efficiency, increase productivity, and gain a competitive edge in the market. Assessing current technological capabilities, implementing a step-by-step approach, addressing challenges, leveraging data and analytics, upskilling the workforce, and measuring success are crucial considerations for successful adoption. Moreover, keeping an eye on future trends ensures manufacturers stay ahead of the curve and continue to drive innovation in the industry.